The Essential Guide to Silicone Injection Molding Machines for Electronics and Medical Supplies
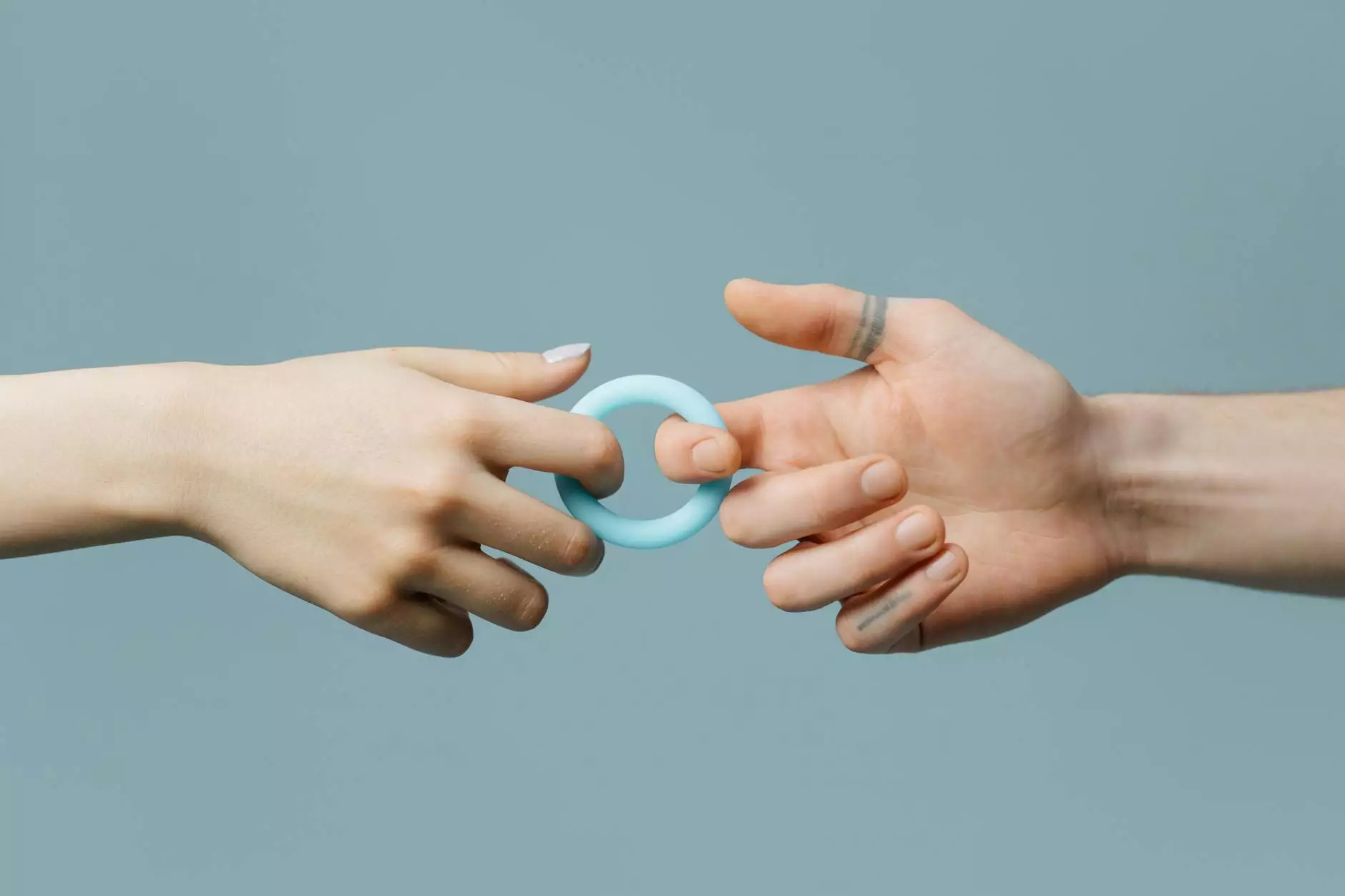
The world of manufacturing has evolved tremendously with the advent of advanced technologies. Among these innovations, the silicone injection molding machine stands out as a revolutionary tool that has significantly impacted various industries, particularly in the production of parts for electronics and medical supplies. This guide delves into the importance, functionality, and advantages of these machines, offering insights into how they can cater to both sectors effectively.
Understanding Silicone Injection Molding
Silicone injection molding is a process used to create parts and components by injecting liquid silicone rubber (LSR) into a mold. This technique is highly favored for its ability to produce complex shapes with excellent dimensional stability and durability. The process involves several steps:
- Preparation: The materials are prepared and heated to the required temperature for optimal flow.
- Injection: The liquid silicone is injected into the mold under high pressure.
- Curing: The material is allowed to cure, solidifying into the final part.
- Demolding: The finished part is removed from the mold.
Why Use a Silicone Injection Molding Machine?
There are numerous benefits to utilizing a silicone injection molding machine, especially in sectors like electronics and medical supplies.
- Precision and Accuracy: These machines deliver consistently precise dimensions, crucial for components in electronics and medical devices.
- High Volume Production: Silicone injection molding enables manufacturers to produce large quantities of parts quickly and efficiently.
- Customizability: The flexibility in design allows manufacturers to create tailored solutions that meet specific requirements.
- Durability and Longevity: Silicone components are resistant to extreme temperatures, UV light, and aging, making them ideal for electronics and medical use.
Applications in Electronics
In the electronics industry, silicone injection molding plays a pivotal role in producing various components, offering both functionality and aesthetic appeal. Here’s a closer look at its applications:
1. Seals and Gaskets
Silicone provides an excellent sealing solution, offering temperature and chemical resistance that is unparalleled. These seals are critical in devices that require protection from moisture and dust.
2. Molding of Keypads and Buttons
Soft-touch silicone keypads are increasingly popular in consumer electronics. The silicone injection molding machine ensures that these components are not only functional but also comfortable and responsive to touch.
3. Insulation Components
The electrical insulating properties of silicone make it suitable for use in components that need to withstand high voltages while preventing shorts and other electrical failures.
4. Housings for Electronic Devices
Silicone moldings can create protective housings that shield sensitive electronic components from environmental factors, enhancing the longevity and reliability of devices.
Applications in Medical Supplies
In the medical sector, the use of silicone injection molding has transformed the production of critical components. Here are some key applications:
1. Medical Devices
Silicone is biocompatible and versatile, making it suitable for use in devices such as catheters, valves, and other medical instruments that come into contact with body fluids.
2. Surgical Tools and Implants
Medical molds can be created with precision, allowing for the production of surgical tools that require complex shapes and sizes. Silicone’s properties help ensure the durability and functionality of these tools.
3. Laboratory Equipment
Silicone seals and gaskets are imperative in laboratory environments to maintain sterile conditions and prevent contamination during medical experiments and procedures.
4. Patient Care Products
Silicone injection molding is used in producing various patient care items, including tubing, molds for prosthetics, and orthopedic devices that improve patient comfort and recovery.
Choosing the Right Silicone Injection Molding Machine
When selecting a silicone injection molding machine, several factors must be considered to meet your production needs:
1. Machine Size and Capacity
Your choice should depend on the volume of production required, along with the dimensions of the products you aim to create. Larger machines can handle high-volume production, but smaller models may suffice for specialized, low-volume tasks.
2. Material Compatibility
Ensure the machine is compatible with the specific type of silicone you plan to use. Different formulations require different processing capabilities.
3. Precision and Speed
Look for machines that offer high precision and rapid cycle times to maximize efficiency and product quality.
4. Automation Features
Modern machines come equipped with automation features that can help reduce labor costs, enhance precision, and improve production rates.
Conclusion: The Future of Silicone Injection Molding Machines
The rise of silicone injection molding machines has marked a significant shift in the manufacturing landscape, offering transformative solutions for the electronics and medical industries. As technology continues to advance, these machines will only evolve, bringing about even greater efficiencies, capabilities, and opportunities for innovation.
From precision-engineered components that enhance the functionality of electronic devices to biocompatible parts crucial for medical advancements, silicone injection molding stands at the forefront of manufacturing technology. Businesses such as Nolato are leveraging these advancements to maintain high standards in quality and reliability across their product lines, ensuring they meet the ever-increasing demands of the market.
The future is robust for those who adopt silicone injection molding technology, positioning themselves as leaders in their respective fields. Stay ahead of the curve by investing in cutting-edge manufacturing solutions that not only fulfill current requirements but also anticipate future needs.