Understanding Plastic Injection Molding in China
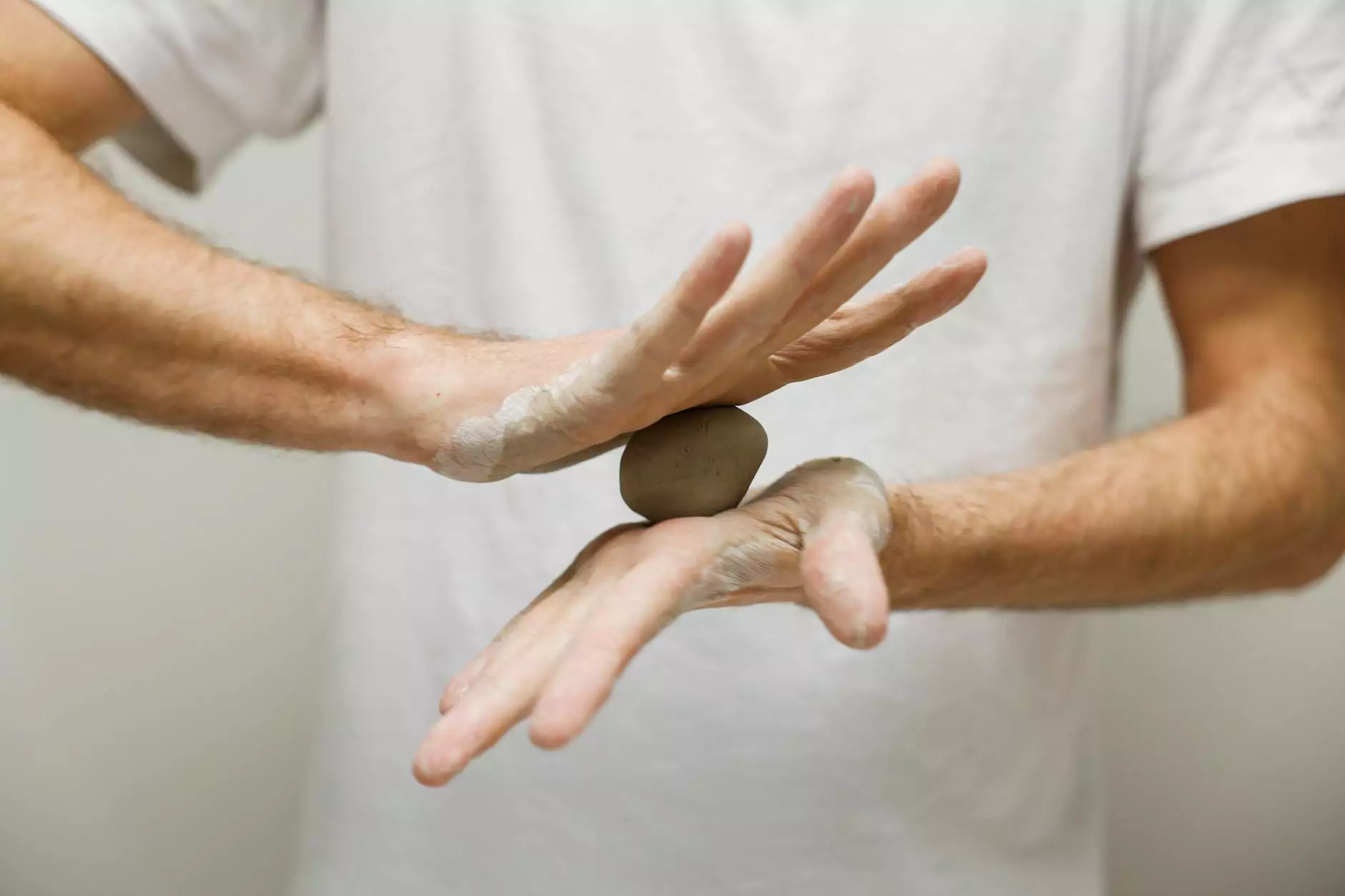
Plastic injection molding has revolutionized the manufacturing industry, making it one of the most critical processes utilized across various sectors globally. In China, a country renowned for its manufacturing prowess, this technique is not only prevalent but also exemplifies high-quality production standards. This article dives deep into the nuances of plastic injection molding in China, underscoring its importance, benefits, and the leading players in this market, such as Hanking Mould.
What is Plastic Injection Molding?
Plastic injection molding is a manufacturing process for producing parts by injecting molten material into a mold. The process involves the following key stages:
- Material Preparation: Raw plastic materials are fed into an injection molding machine where they are melted.
- Injection: The molten plastic is injected into a mold where it cools and solidifies into the desired shape.
- Cooling: The mold is cooled to facilitate the hardening of the plastic.
- Mold Opening: Once cooled, the mold is opened, and the finished part is ejected.
The Evolution of Plastic Injection Molding in China
Over the years, China has emerged as a global leader in plastic injection molding. This expansion can be attributed to several factors:
- Cost-Effective Production: China offers a labor market that is highly competitive, reducing the overall production costs significantly.
- Technological Advancements: Continuous investment in technology has enabled Chinese manufacturers to enhance product quality and efficiency.
- Infrastructure Development: Improved infrastructure facilitates better logistics and supply chain management, further strengthening the industry.
Benefits of Choosing Plastic Injection Molding in China
When it comes to sourcing plastic components, manufacturers often seek out plastic injection molding in China for several compelling reasons:
1. High Precision and Consistency
Modern injection molding techniques allow for high precision in the production of complex components. In industries where accuracy is crucial, such as aerospace and automotive, the ability to produce consistent parts at scale is invaluable.
2. Versatile Applications
Plastic injection molding is suitable for a wide range of applications, including:
- Consumer Electronics
- Automotive Components
- Medical Devices
- Toys and Recreational Products
3. Efficient Production Process
The ability to create large quantities of identical products in a short time frame makes injection molding one of the most efficient manufacturing processes. This ensures that companies can meet high-demand situations without compromising quality.
Choosing the Right Plastic Mold Maker
Understanding the importance of selecting a reputable plastic mold maker in China is crucial for ensuring the success of your project. Here are key factors to consider:
1. Quality Assurance
Look for manufacturers with robust quality assurance processes. Certifications such as ISO 9001 can indicate a commitment to quality.
2. Expertise and Experience
Experience in your industry can be critical. Manufacturers with a seasoned background in your particular sector will better understand your specific needs and challenges.
3. Technical Capabilities
The technical expertise of a plastic mold maker plays a vital role in the production process. It includes their proficiency with advanced machinery and ability to work with various plastic materials.
The Process of Plastic Injection Molding in Detail
To gain a better grasp of how plastic injection molding operates, it's essential to delve deeper into each phase of the process:
1. Design Phase
This initial phase involves creating detailed designs and specifications for the mold. CAD (Computer-Aided Design) is widely used to ensure precision in this step, allowing for the creation of complex geometries suited for automated manufacturing.
2. Creating the Mold
The mold is typically made from high-grade steel or aluminum. The manufacturing of the mold can take several weeks, depending on its complexity. This phase is critical as inaccuracies in the mold can lead to defects in the finished product.
3. Injection of the Material
The molten plastic material is injected into the mold at high pressure. This ensures that the material fills every nook and cranny of the mold, resulting in a consistent part.
4. Cooling and Ejection
Once the mold is filled, it is cooled. The amount of time needed for cooling depends on the type of plastic used and the size of the part. After sufficient cooling, the mold opens, and the finished part is ejected.
Challenges in Plastic Injection Molding and Solutions
Despite its many advantages, plastic injection molding does come with certain challenges. Here are some common issues and their solutions:
1. Warping
Warping occurs when parts cool unevenly. This can be mitigated by optimizing cooling channels within the mold.
2. Short Shots
Short shots happen when the mold does not fill completely. Adjusting the injection speed and pressure can help resolve this issue.
3. Surface Defects
Defects like burn marks or sink marks can result from inconsistent temperature control or poor material flow. Careful monitoring of the molding conditions is essential for avoiding these problems.
Conclusion: The Future of Plastic Injection Molding in China
As the demand for high-quality and cost-effective manufacturing continues to grow, plastic injection molding in China is set to see even more advancements. With a focus on sustainability and technological integration, the future looks promising. Manufacturers like Hanking Mould are leading the way by embracing innovation and quality, ensuring they meet the evolving needs of their clients.
In today's competitive market, choosing the right partner for plastic injection molding is paramount. With the right knowledge and resources, businesses can leverage China's capabilities to excel and innovate in their respective industries.
plastic injection molding china